The Essential Guide To Military FOD Prevention
Protecting Military Aircraft From Foreign Object Damage
Anyone who has spent time working in the military around aircraft has heard about Foreign Object Debris and Foreign Object Damage. So taking into consideration the exacting FOD prevention controls put in place by military organizations over both their personnel and their work procedures, it is sometimes difficult to understand how their aircraft continue to suffer from damage caused by FOD.
Work areas are kept scrupulously clean and well maintained, tools are kept in good condition and rigorously controlled, and personnel are specifically trained and regularly refreshed on the hazards of FOD and the need to be vigilant — even those not associated with aircraft operations.
So why then have three nations this author has direct knowledge of lost military aircraft in the last ten years from FOD to fan or compressor blades on turbine engines?
It is not enough to understand just what FOD is, but we need to understand how it occurs, understand the specific hazards unique to the many areas of work, and develop tailored prevention activities that aim to eliminate military FOD.
Understanding military FOD is the first important step we must take before enforcing relatively simple and routine preventative measures. Indeed, if we understand the mechanisms of FOD, we establish the first and vital foundation block on which to build a prevention program to minimize the operational, economic and human costs of FOD.
Getting Started
FOD means different things to different people and can show itself in many ways on an aircraft and its components.
FOD Is A Threat To Aircraft Tires
When an aircraft taxis down a runway, the tires may pass over a stone or object that could cut the tread and lead to subsequent failure with an immediate puncture or, more likely, when the tire is rotated and loaded on take off.
One of the most notable FOD incidents occurred on July 25th, 2001, when a French Concorde, Flight AF4590, while taking off from Paris, reportedly taxied over a piece of metal shed by another aircraft. A main undercarriage tire was cut, and the subsequent failure on take off shed a large piece of tread that hit the wing and caused a hydraulic shock wave in the fuel tank.
A massive fuel leak ensued, to be ignited by an electrical arc from wiring in the undercarriage that had been damaged by the tire failure. Further damage was caused to hydraulic pipes and controls, stopping the undercarriage from being retracted and causing a loss of power on the number one engine and the second to cut out. At this stage it was too late to abort the take off.
In the critical first moments of flight, fighting to overcome the high drag of the supersonic airframe, the aircraft was unable to gain height or speed. Fire engulfed the wing, engines and flying surfaces; the aircraft flew for less than three minutes before it crashed into a hotel in the small town of Gonesse killing 109 on board and four on the ground.
Aircraft Tires Are Exposed To Extreme Forces
Whilst the tire loading on take off is high, especially at the Concorde’s very high take off speed — about 250 miles per hour compared with 170 miles per hour for most other subsonic aircraft — that loading is magnified many times over on landing.
On landing, the wheel is shock loaded by the descending weight of the aircraft and the instantaneous acceleration to well over 100 miles per hour. A burst at this critical moment can lead to sudden loss of control and force the aircraft off the runway.
Burst Tires Lead To Loss Of Aircraft Control
Early in my career, I was on a detachment at RAF Waddington, near Lincoln, England, when an F4 Phantom blew a tire on landing. The aircraft immediately departed the runway, ran onto the grass in the center of the airfield, and sped toward cabins where the ground crew and I were operating.
The pilot fought with the controls but as the aircraft sank into the muddy field, he was unable to adequately retard the speed or, more importantly, steer the nose wheels to control the direction. At less than five hundred yards from the buildings, the pilot was faced with a split-second decision, and he and his navigator ejected.
The aircraft carried on its path, held firmly in its mud tracks, but as it continued to sink up to its axles and the landing gear doors, its speed rapidly declined and it came to rest a few hundred yards short of the buildings. Several seconds later the pilot and navigator, both now under parachute, landed safely on the airfield.
Although no one was hurt, it is an event that I will never forget and one that has served as a reminder of the hazards of aircraft operations and of FOD.
FOD Is A Threat To Turbine Engines
For the uninitiated, turbine engines can rotate at over ten thousand-rpm, and when a tiny piece of debris like a piece of safety locking wire or stone get ingested it behaves in a ballistic manner, striking the compressor blades as if fired from a gun. Depending on material grade, shape and size, the debris can cause damage to the first blade or any part of the intake they strike.
As the debris passes through the engine, its many contacts by fan blades can break it into smaller chunks or the debris can liberate pieces from the blades that multiply the debris field and increase the size and quantity of the damage.
I have seen a small nick on the first stage of the fan and seen the rear stages of the compressor and most of the turbine rotors completely decimated, as if someone had taken barber shears and clipped the blades from the disk. Where the blades are highly loaded or are subject to vibration — sometimes referred to as HCF (High Cycle Fatigue) — the damage to the blades can grow rapidly to a crack and subsequently fail.
Catastrophic Engine Damage
Although engines are designed to contain failed blades, a blade failure can lead to the total destruction of the engine. Indeed, many posters exist that show how the ingestion of a small metal screw, which costs just a few pennies, can cause damage requiring the complete replacement of the engine, which costs many millions of dollars.
However, it is not just hard debris that causes damage; a plastic bag can behave like a large sheet and blank the intake, stalling the airflow across the blades and causing the engine to surge. Engines can usually tolerate a surge — a reversal of the airflow — but, depending on severity, a surge can deform blades and necessitate the replacement of the engine.
Foreign Object Elimination Is Our Mission
It is easy to see why we must control debris to maintain safety and reduce costs. FOD is correctly seen as a flight safety risk, and everyone is responsible for keeping that risk as low as possible.
Picking up debris that could migrate onto airfields is the first step that could avert a disaster.
True, seldom does FOD result in a disaster, but it can be one link in a chain of events that, if left unbroken, could result in the failure of an engine, loss of aircraft and taking of life. Breaking that chain could be as simple as picking up litter. A key area to achieve maximum benefits is through training and education. More can be done if we target areas for improvement and coordinate increasingly limited resources to reduce problems and get the best return of investment.
Sources and Mechanisms of FOD
Understanding how engines ingest debris is important.
Vortex Ingestion
Engines ingest debris through vortex ingestion. This phenomenon can sometimes be seen during cold and wet conditions when water is drawn up into the vortex and ingested.
A vortex is created by the disturbance of airflow around the intake mouth. In normal conditions, airflow is pulled from all around the intake. As the airflow is drawn from the rear of the intake, and as the flow interacts with the ground plane, a Venturi Vacuum Effect is created by the ground and underbelly of the aircraft or intake. A vortex initiates due to the presence of a prevailing wind that blows at an angle to the intake face and forms a shear vector that causes the airflow-to-ground-plane interaction to swirl.
A vortex seen on a Boeing C17 Globemaster
Vortex air flow illustration
The speed and strength of a vortex is dependent on the speed and strength of the ingested airflow and wind vector. Preventing a vortex from forming can be as simple as pointing the aircraft into wind.
When a vortex forms and attaches to the ground, the periphery behaves like a rotating brush sweeping objects out of its path. However, if the objects were trapped, held in place between the gaps in the concrete and the eye of the vortex passed over them, then the objects may be picked up in the negative pressure at the eye and be ingested.
Therefore, special attention needs to be placed on cleaning the gaps and ensuring that they are fully filled with sealant to avoid providing a temporary resting place for debris.
Want to learn more? Contact us for guidance on developing your FOD prevention program!
Aircraft Generated FOD
Aircraft generated debris is especially noticeable on supersonic intakes that have auxiliary air intake doors; these doors supplement the intake airflow when the aircraft is stationary, or at a slow forward speed or vent air when traveling at high speeds when the intake is in ram effect.
Older supersonic intakes have many moving parts — ramps and doors — that control the airflow though movable ramps that form shock waves to slow the airflow in supersonic flight or by bleeding air to present the engine with smooth controlled airflow at the right speed. The ramps and some doors are usually hydraulically operated and are supported by a series of mechanical components and switches that, in turn, have their own access doors, hatches and fairings. The access doors are secured with a range of fasteners and locking devices. These fasteners and locking devices have proven to be frequent causes of FOD.
Secondary Inspection
Special FOD prevention measures can be put in place, which call for an independent inspection by an unconnected third party trade person, after any work that involves panel removal has been completed. The inspector would check for fit, form and function — as is usual with an independent inspection — and ensure that the panel and its associated fasteners do not become a debris hazard.
Furthermore, it may be worth considering that any access bays be cleaned and checked prior to being closed; this could be as simple as using a vacuum and a flashlight. Further security and safety can be inexpensively applied. For years, when removing panels, the military has used fastener bags to secure loose fasteners and attach these bags to the panel once removed and placed on a parts stand.
Remember, what may seem obvious to the trained eye has to be learned by someone new to a skill or work area, and we should share experience rather than make the uninitiated learn the lesson again, especially where safety is concerned.
The Tornado auxiliary air intake doors are shown adjacent to the intake, under the leading edge of the wing where the wing joins the fuselage.
Tornado intake viewed from the engine bay looking forward to the air intake lip. The white blemishes show damage that has been dressed out.
Thrust Reverse
Perhaps the prime contributor to FOD on fast jets is thrust reverse. Thrust reverse directs engine exhaust air forward to provide a braking mechanism. Thrust reverse disturbs the smooth airflow around the intake and ground, and can pick up debris and provide the lift to project particles into the strong airflow around the intake lip, down the intake and into the engine.
Many airlines also use thrust reverse to help control speed on landing and prevent the aircraft brakes from overheating. The use of thrust reverse has to be strictly controlled and limited to forward airspeeds where particles cannot be thrown forward and ingested. Even at slow aircraft forward speed, the hot gas from the exhaust can be re-ingested and cause engine stall and surge.
Human Generated
History has proven that human-generated debris is a main contributor to FOD.
Unfortunately, intakes and intake lips do provide a convenient resting place for temporarily storing articles. High or low set, intakes remain a feature that must be checked and rechecked prior to engine start.
RAF Phantom F4 from 74 Squadron
Engine Intakes Are An Ongoing Risk
On the VC10 transport aircraft, the intakes are simple bell-mouth shapes that form part of the pods that house the engines; they are fitted two on each side of the tail, about 12 feet off the ground.
During maintenance to the intake, a small pot of rubberized sealing agent was applied to the outboard intake while the inner was used as a stand for the pot. Again, the work person was distracted and the pot was forgotten.
During the subsequent pre-flight inspection, the intake was checked from the ground but because of the height of the intake, the intake lip made the pot invisible to both the aircrew and ground crew. On engine start up, the pot was drawn into the fan face and severely damaged the engine, which led to its replacement and overhaul.
It Only Takes A Momentary Distraction
Distractions like the ones above are common in aircraft operations. Even the most able people can be forgetful when occupied with multiple tasks and faced with a decreasing timeline.
Accordingly, tool control and the control of what are classed C stores — screws, bolts, seals and washers — were brought into effect; tool control is mentioned later under its own heading.
While maintainers are trained and undergo refresher training to keep the dangers of FOD fresh in their memories, many visitors to aircraft operating bases will not have come across the acronym and may not understand the associated hazards. Strangely, many contractors with access to aircraft work areas may never get briefed.
Fortunately, military in the USA and UK generally recognize this loophole and have provided briefings and instructions to contractors working on their units. Moreover, each station has a FOD Prevention Officer who knows engine maintenance and has the ear of command and a nominated prevention officer for the whole service. This command organization helps provide visibility and takes action to help prevent recurrence of incidents.
Coveralls Required
Lastly, on human-generated FOD, the Royal Air Force insists that aircrew and ground crew keep their pockets free from objects by providing working coveralls that have no buttons and personal lockers that are secured with a combination lock and used for clothing and small items like keys and money.
In some areas, such as the flightline, additional small personal item lockers — similar to lockable mailboxes — are available to secure frequently used small items. In addition, smoking is not allowed in the work areas to maintain safety. For engine intake inspections, where the inspector has to enter the intake, many bases have special pocket-less coveralls.
Debris Control
Understanding the mechanisms of ingestion should help you visualize how debris gets ingested and provide the knowledge to generate effective working practices.
Areas of work must be kept scrupulously clean. Any breakdown in the paved surfaces must be quickly repaired. Moreover, if at all possible, the damage should be isolated and cornered off or cleaned and checked on a regular basis to ensure that particles are not being generated. During the repair activities, debris can be a problem and work personnel should be thoroughly briefed, and the area checked, as the repair progresses. In recent years, work sites have been surrounded by plastic mesh that prevents debris migration. Moreover, as it is typically bright orange in color it provides a visual notice to avoid the area.
On many bases, civilian contractors carry out repairs, and it is imperative that they be briefed about the dangers posed by uncontained debris.
Contractors Should Be Advised Of The Risks And Supervised
Concrete runways are routinely overhauled and, after many landings, rubber tire marks have to be removed; on one Air Force Base, a civilian contractor carried out this operation over a weekend. The contractor was probably not briefed or supervised and used metal balls — shot blasting — blown onto the marks at high speed. The runway was made up of twelve-foot square concrete blocks. The expansion joints between these blocks were sealed with asphalt sealant.
The contractor cleaned the marks off the runway but left thousands of metal shot immersed in the sealant. When aircraft operations commenced early the next week, the shot was lifted, ingested, and resulted in the removal of several engines from combat aircraft.
It was a very costly lesson to learn, not just from a cost perspective but the loss of sorties and considerable disturbance to operations — both of which have no associated cost to the military, but obvious considerable value.
The need to keep operating and maintenance areas clean cannot be overstated.
Mechanical sweeping and ad-hoc FOD Walks by personnel are effective ways to minimize debris. Sweep and inspect as often as possible.
Following the FOD Walks, the debris found can become an exhibit to be displayed on notice boards or custom FOD displays that can and should be moved to different areas of work. Good posters and photographs can have a great impact, but this impact is lost over time as the posters become like unnoticed old wallpaper. To work to maximum effect, posters should be routinely changed. Sharing posters and ideas with other services or other nations can bring new ideas and generate new interest.
Want to learn more? Contact us for guidance on developing your FOD prevention program!
Tool Control
Tool control is an effective way of accounting for all tools that are used on aircraft.
Many years ago, I worked alongside contractors who were making some modifications to aircraft that required the engines to be removed; I helped them with this work.
Each person on the team had their own tools and carried them in a variety of containers. The quality of the tools varied, as well as the containers, and they were loosely held sometimes several layers deep in each tray and perhaps as many as a hundred tools in a five-drawer tool box.
With no standardization and no requirement to check tools at the end of the working day, it was each individual’s responsibility to account for his tools. With hundreds of tools to check and workers helping themselves to others’ tools, it was impossible to account for them.
In those days, this situation was not an isolated incident and many companies worked with a similar regime. Not surprisingly, when the aircraft were delivered to the Royal Air Force, tools were sometimes found along with other maintenance equipment.
During that same period, I remember talking to some military maintainers who worked on the Vulcan bomber; they had just gone into a wing fuel tank and found a workbench that was probably used to help fasten the fuel-tank bag in place.
Incidents like this eventually led to a change in working practices that saw the introduction of tool control in the aerospace industry.
Tool Control Has Come A Long Way
The military have for many years used tool control to great effect. They procure premium grade tools; etch them to uniquely identify them to a station, squadron, flight and toolbox; and color-code them for quick identification on the units. Furthermore, no personal tools are allowed in the work place.
In the tool containers, each tool has its own resting place that is shadowed/highlighted to indicate its absence; in recent years sheet foam has been used to layer each drawer or tray and is cut to house each tool.
When a tool is taken, the worker using it places a numbered plastic tag against the tool space or shadow. The tag identifies who is using it. Moreover, each tool kit is booked out to the aircraft that it is being used on, using tags controlled by the engineering operations rectification controller; this person checks that all the tools have been accounted for before he signs the aircraft over to operations for flight-line servicing.
When a work task is completed, the person completing the task checks that all his tools have been returned and that all his tags are accounted for; maintenance personnel sign for completing these checks as part of the work order paperwork.
All tools are controlled through tool stores, which keep specialized tools, small and specialist equipment, cleaning rags and other general-purpose equipment. Each item — tool, box and hardware — is identified in the same way as the tools in the toolboxes and accounted for in the same way.
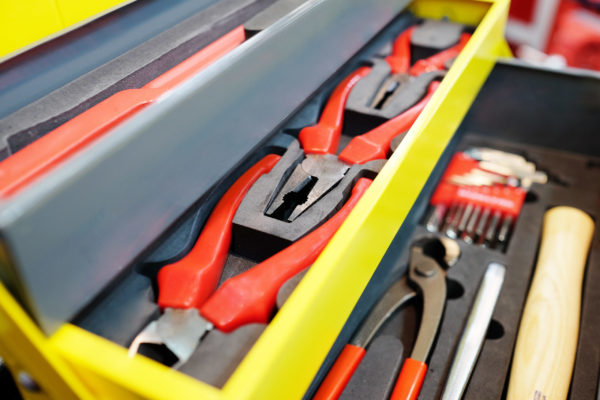
Tool Accountability
A person is given the duty of controlling the tools — a job often held by the squadron or flight supplier/logistician — and serves the tools over a counter. The supplier checks the completeness of the tools and tool kits, and performs a second check after the tradesperson; in addition, they perform tool inventories at least at the start and finish of each day.
If any tools are missing, a check is done immediately using the tag system to identify the aircraft it was being used on and the person using it. If that person cannot find the tool nor has any recollection of where it was last used, a larger scale search is carried out. At this time, the trade supervisor or trade manager should be informed and a thorough search initiated.
In the unlikely event that a tool is still not found, an all trades search should be completed using zoned areas of the aircraft. The removal of access panels and equipment should also be considered. Control runs and controls should be checked and independently confirmed to be free of restrictions. Inspection devices — lamps, borescope and even x-ray — should be considered.
If all this does not find the tool, then the senior engineer or maintenance officer would have to consult with the chief engineer on the station and consider a check flight or flight test. The test is a single flight that is recorded in the aircraft Limitations Log and involves a period of inverted flight to attempt to free the tool from its hiding place.
On landing, further inspections are carried out in the same way as originally completed. If still not recovered, an entry is made in the ADF (Aircraft Deferred Faults) Log that will call for further inspections of the suspect area on the next scheduled maintenance. If it is not found then, the ADF entry is cleared. This situation seldom occurs, as there are many checks and balances in place to maintain safety.
An effective Tool Control Program is vital to flight safety, and is evaluated regularly by quality assessment teams from the squadron, unit, wing, and command. These teams ensure correct procedures are in place to control hazards and prevent problems. In past years, these checks were to confirm standards and look for any discrepancies. Today, they are more to ensure that systems, orders, and training are in place and effective. It is more a top-down than bottom-up approach and has won the support of the management and workforce.
Reporting
Having worked for both the RAF and USAF in command and staff appointments, I have witnessed the benefits of comprehensive reporting. Through studies carried out originally at DERA (Defense Evaluation and Research Agency) and then later at DSTL (Defense Science and Technology Laboratory), information is obtained on every FOD occurrence. The information includes the sortie details preceding the event, weather, location, and debris detail — if known or presumed — and statements from the associated squadron maintenance officer, station FOD officer, and chief engineer.
The reports are fed back to command and to the RAF FOD Prevention Officer for consideration of any follow-up action or visibility. Every six months, the Reports are collated, and a written report is published for dissemination to every station and FOD officer. The reports can provide trends indicating problems, either on a unit or with an aircraft type, which help target a response and prevent recurrence.
Moreover, the design authority — engine manufacturer — can also use the reports when considering modification or future designs. Debris indentations are identified throughout the engine and, through repeated events, designers can determine where blades are most susceptible to damage. Thorough reporting is essential to any FOD prevention program. The system operated by the RAF is perhaps the most comprehensive in the world.
On Deployment
While on military deployment and operating in a new environment, extra vigilance must be taken to ensure a FOD free operating location. In many cases it is a short notice deployment with no forward inspection, and the parking ramp is a transit setting with many different aircraft from different commands. There may be no central FOD control person looking at the whole picture. That leaves everyone on their own, so here are some tips on reducing the danger to your aircraft: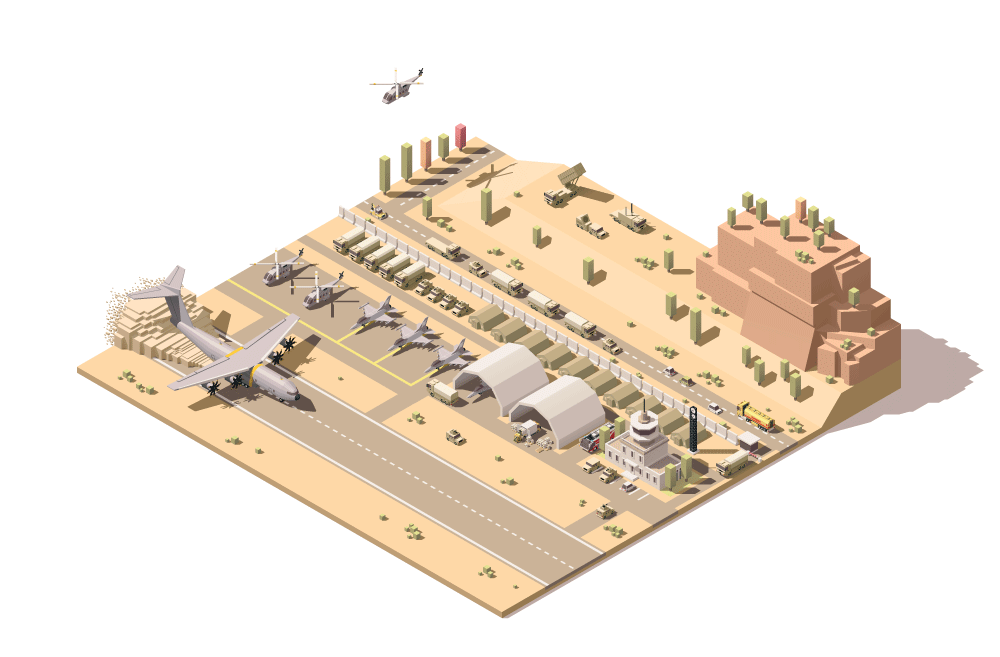
-
- Bring your own FOD prevention tools with you. FOD Containers, Magnetic Sweepers, etc.
- Take a good look at aircraft positioning — not just yours. Are their aircraft positioned in such a way that their exhaust could be tossing objects towards your aircraft? Also consider engine maintenance run-up areas and how they might affect your aircraft.
- Be positive and diplomatic when dealing with the home base. The wrong perception of your organization could create new problems.
- What is being used for snow removal at home base or on deployment? Many locations may still be using metal street sweeper type brushes, which leave a trail of metal bristles behind. Consider switching to nylon brushes or initiate a sweeping program to insure their removal.
- Develop a deployed FOD Prevention Handbook for the person tasked with managing the program at the deployment location. Basic information on this subject is available on this website. Since the regular Wing FOD Program Manager at your home base may not be there, insure the person assigned as the deployed FOD Program Manager understands the importance of FOD Prevention and is suitably motivated.
Want to learn more? Contact us for guidance on developing your FOD prevention program!
On Base
Runway sweeping is usually carried out by mechanical sweepers to clean the surfaces by collecting debris using a vacuum, brushes, and/or sometimes, magnetic media. Most operating stations have a sweeping plan that virtually segments the airfield into blocks that are attended to at least weekly.
In addition, runway sweeps can be requested on demand and are worth considering after repairs, extensive aircraft work or following inclement weather — like strong winds and rain —that can move debris onto the airfield. Although some airfields use road sweepers, new specialized FOD sweepers are available that are much more effective. Some equipment can clean surface areas and down between the gaps in the concrete blocks, keeping flight operations areas scrupulously clean.
Airshows And Open Houses
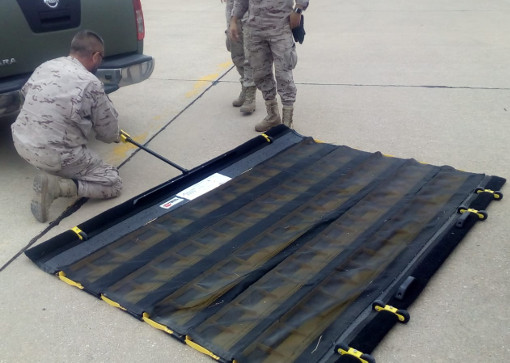
Many military airfields have open days during which vast crowds are allowed onto the airfields. The airfields are transformed into fairgrounds with external catering and amusements brought in to keep the visitors fed and entertained. Flying displays are usually scheduled for the busiest times. Special attention is required to keep the operating areas free from debris, especially on days where strong winds can blow litter onto the field. Hooded litter bins should be freely available and placed close to the generating sources, like the food and drink stands.
In addition, at the forward edge of the crowd line, netting, like that used by builders or around airfield repairs, can be employed to prevent litter migrating. During the day, work teams should be used to collect and empty litter into lidded trash bins or contained bulk waste disposal areas.
At the end of the day, or before operational flying commences, the airfield should be walked for FOD. Everyone should be employed in this task to ensure that all the litter and other human-generated debris is removed. Furthermore, on the aircraft used for static displays, the aircraft should undergo checks for loose articles by all trades and disciplines.
Management Responsibility
In the military, management is sometimes overlooked in the face of strong leadership. Leaders take a dominant role, but managers ensure that procedures are set and practiced, modified, and improved. However, in many areas, like maintenance and logistics, the leader and the manager are the same and often take the form of a commissioned officer or senior non-commissioned officer.
With these people, the responsibility for safety is always a priority, but this is balanced against operational needs and cost; it is pointless having the safest aircraft and best working practices if the aircraft cannot fly. Conversely, you cannot have the best mission launch rates at the expense of safety and aircraft loss.
A Balancing Act
With FOD control, the manager has to assess risk, implement and enforce standards, and check to see that working practices continue to be effective. These practices are often delegated; however, while the role may shift, the responsibility remains.
Consequently, managers must be reactive in dealing with damage and proactive in dealing with prevention. They must commit and support at every level and be prepared to assist as well as enforce. In my education as a young engineering officer, my mentors used to say “GOYA — Get Off Your Ar** —” and see firsthand what the problems are. Talk to the people that are at the front line where the “rubber meets the road.” These people are the ones that use the orders that you want to put into effect, and they will provide the feedback. They know the how, why, what, and when, the effectiveness and the best way forward.
However, be assured that they will not write to you with their concerns. Equally, irrespective of how well an order is written, they will not put into action something that is stupid or causes them unnecessary hardship. The best orders are those which they help form and those that take their needs into account. The best managers have the ability to understand the needs of everyone and support the key initiatives and practices that have best effect.
Moreover, these managers are quick to praise and recognize outstanding effort with award and reward. In FOD Prevention, award may be a certificate and reward maybe public recognition of having “gone that extra mile.” From my largely military perspective, I have seen that the military are at the forefront in leading and implementing FOD Preventative measures, but whether the area of concern is commercial or military, I know that it takes a committed team to have the best effect.
Everyone’s Responsibility
“FOD is everyone’s responsibility” is often repeated, but I often wonder how many take the saying seriously. There remains a pressing need to actively minimize debris and report activities that could lead to damage or follow-up events to help prevent recurrences. Furthermore, each of us can help to eradicate the problem. Everything helps, no matter how small. Pick it up, talk about it, draw or place a poster to illustrate it, share ideas, participate and work together.
It is everything about being part of a team. Irrespective of where we work, we all have a part to play. If we are in any way connected with flying or the support of operations, we can help. Even as fare-paying passengers, we have a duty of care and consideration. Do not throw litter and do not throw debris where it can migrate into the path of an aircraft.
Think outside the boundaries of your job and be prepared for the unexpected. Be willing to help. One man against FOD is good, but a team effort is better. Work with the team and build a team through which we will all benefit.