Wherever aerospace products are manufactured or flown, a philosophy and culture of FOD Prevention spanning the entire operation is vital to assure product integrity, reliability, and cost savings. Implementing a strategy to minimize FOD incidents takes time and effort as well as cooperation from almost everyone in the company.
Since you put in the time, you want to make sure that your approach to preventing FOD is effective. The only way to be sure of this is through careful monitoring of FOD incidents as well as the efforts you are making to address and prevent them.
Suggested Resources
Check out our articles on What is FOD? or How to Set Up a FOD Program for more information.
“If you can not measure it, you can not improve it.” – Lord Kelvin circa 1880
Purposes of FOD Incident Monitoring
Monitoring FOD incidents, training, and programs serves several purposes. First, it tells you whether your efforts are effective in reducing the number or severity of FOD incidents in your business. Second, it sheds light on the areas where you can still improve or make changes.
Perhaps you need to spend more time training a certain crew to deal with FOD, or maybe you find that you still need to make some more changes to your processes to reduce the number of instances of FOD. Without consistent careful monitoring, you have no way of identifying ways to continuously improve your FOD prevention program.
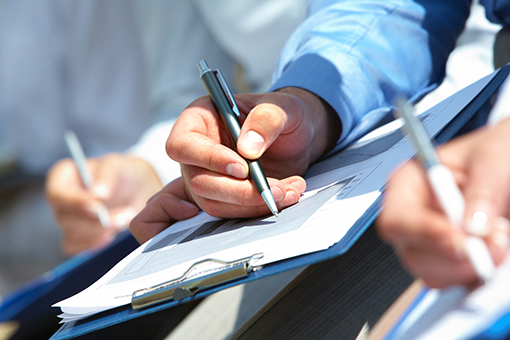
Collecting Incident Data
Monitoring FOD incident monitoring requires that you collect data regularly. This data must be formatted consistently and in a way that’s easy to interpret. As a part of your FOD plan, you should identify which components to track in your plant or equipment.
Of course, this involves keeping track of the number and date of each FOD occurrence, as well as other contributing factors that vary by business.
You’ll likely want to track the crew members involved, the time of day or the incident, the equipment used, and many other business-specific factors.
It’s also important to keep data on your processes to prevent FOD. Keep track of who receives training and when. Track which workers are involved in preventing FOD incidents.
You’ll likely want to designate specific employees to be responsible for this incident data collection and maintenance. Delegating this task to one or several people generally ensures that data is collected and maintained more consistently.
Other Sources of Data
It’s important to be resourceful when looking for sources of FOD data, too. Review all incident reports related to equipment failures for signs that FOD and/or FOD program process failures may have been contributing factors to them. Track these separately in an Excel sheet for easy access.
You can also poll customers about FOD incidents with products you have delivered to them. Pay close attention to feedback to make sure you get the full story.
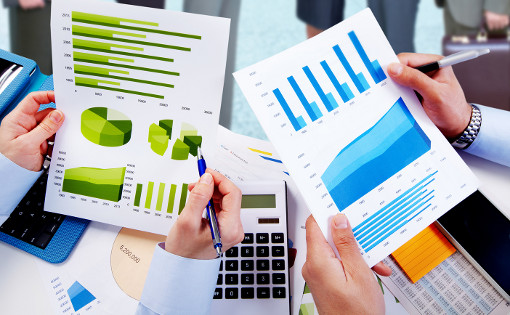
Charting Your Progress When Monitoring FOD
Once you have collected and maintained your FOD incident data, the next step is to consolidate and display it in a meaningful way. This will vary by business, but some ideas are as follows. Create a bar graph of your FOD incidents data, showing the total number of incidents each month.
Shade the bars accordingly to show how many are contributed by each division of your company. Another idea is to plot the number of incidents against the number of hours of FOD training provided to each crew member.
Make Plans for Improvement
After examining your raw incident data and the charts you create from it, the last step is to identify problem spots in your processes to prevent FOD. Perhaps you notice that Division 1 has received 20% less training, and has had 4 more FOD incidents over the last 12 months. Online oyun dünyasında keyifli bir deneyim yaşamak isteyen oyuncular için en önemli kriterlerin başında güven gelir. Lisanslı, hızlı ödeme yapan ve kullanıcı verilerini koruyan güvenilir casino siteleri , bu alanda ön plana çıkıyor. Geniş oyun seçenekleri, 7/24 destek ve mobil uyumluluk sayesinde hem yeni başlayanlar hem de deneyimli oyuncular gönül rahatlığıyla oyunlarını oynayabiliyor. A corrective action would be to provide more FOD training to Division 1 employees.
Preventing FOD requires continual attention to detail. It’s an ongoing process and collecting data for careful monitoring that helps you decide which steps are next in that process.