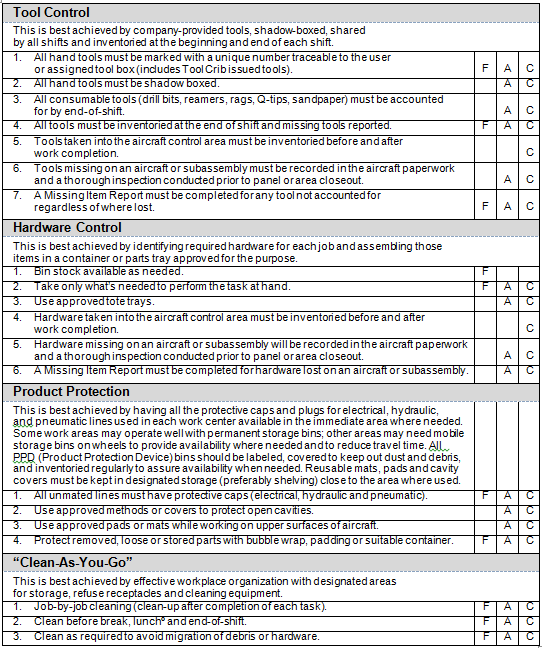
FOD Table
Letter Codes for the three control areas are:
F = Fabrication
A = Assembly
C = Checkout
Manufacturing products for aerospace differs from other assembly operations by the strict requirements of product integrity and the processes used to assure safety and reliability.
The potential of introducing foreign object debris in manufacturing during fabrication is very high.
Without even considering tools, employee personal items, drill filings/chips and all the other possible contributors to FOD in manufacturing facilities, just the number of fasteners used to assemble the structure and install components can measure in at hundreds of thousands.
It takes only one fastener in the wrong place to cause an incident resulting in loss of the aircraft and/or loss of life. Supervisors and workers cannot merely be told or expected to build a FOD free product, including FOD free assemblies manufacturing.
In a manufacturing environment, cost often drives schedule. After all, to continue building any product it must be profitable. FOD controls in manufacturing facilities often impact costs and schedules. Implementation and maintenance of controls should be planned and formalized as part of the product manufacturing scheme—not as an unpleasant afterthought when things go wrong.
But what about the savings? They’re yours to claim with a commitment to FOD controls. Once established, an effective program reduces rework, scrap and incidents. Want increased customer satisfaction and sales? What about reputation and the pride of building the best product you can? What about beating the competition and increasing market share? Even if an effective FOD Program or Procedure hasn’t been planned and implemented previously in your operation, the time to start is now. FOD control is quality. FOD control is safety. FOD control is integrity. The savings and benefits far outweigh the costs and time expended.
Although manufacturing controls are necessary to prevent the introduction of FOD, the design of the structure and sub-assemblies plays a vital role in the ability to inspect and remove foreign objects during and after assembly. If fortunate enough to plan a new product or assembly line, Design Engineering should incorporate FOD removal procedures into each aircraft zone. A “Design Checklist” with buy off from Manufacturing Engineering is required.
Design is your first and best opportunity to eliminate FOD from the delivered product by planning for inspections, cleaning of cavities and designing out entrapment areas. For older/ existing structures that didn’t plan FOD Prevention into the product, modifications and overhaul planning should require FOD inspection/removal steps to be incorporated into each package.
Some aircraft contain known FOD entrapment areas that are impossible to inspect or clean. These aircraft are accidents waiting to happen and should be redesigned and modified or dropped from service. Knowing of foreign objects in a flight article and/or the potential for damage is next to sin — it cannot be ignored. The responsibility to identify and report the potential for FOD lies with everyone involved in any phase or process. Management should solicit all employees to report potential FOD as they would any safety or quality concern, and should request design changes if feasible to assure product integrity. Repeat: Design stage is the very best opportunity to keep FOD out of the delivered product.
Management must be supportive of and responsible for the FOD Prevention Plan and its implementation. All applicable policies and procedures, training programs, and operational guidelines must include reminders for FOD prevention procedures and controls.
Management must demand effective corrective action for FOD incidents, problem areas, and negative trends. Without upper management support and encouragement, FOD Prevention is “just another program” or passing notion. Strong, deliberate enforcement and backing are necessary if compliance is to become reality.
Within the organizational scheme, the FOD Program manager or coordinator should have similar rank and authority as the Safety or Quality manager, and should be independent from manipulation or bias from other operational units (such as Assembly or Test). Some successful programs have FOD reporting to the Quality or Safety manager, but FOD Program management deserves the same status and recognition as those disciplines.
Having all three placed within one organizational unit may be the best profile as they share many similarities such as: inspections for compliance, “shut down” authority, data collection/trends, customer interface, awareness (promotion) and employee recognition.
Organizational Chart
SOPs (Standard Operating Procedures) and operational guidelines must be developed and kept current. FOD inspections are required for panel closeouts, manufacturing process spot checks and procedure compliance. Investigations of FOD incidents/mishaps can only be performed by an organization with an unbiased eye. FOD inspection/removal equipment must be operated and maintained by trained specialists. Audit and incident data must be collected, entered into a database, information sorted into various report formats, posted on status boards and distributed to key personnel. Corrective actions for problems/issues must be tracked and verified as effective. Meetings and briefings must include both management and workers. FOD training programs must be developed and conducted annually (minimum requirement). Awareness and recognition programs must be administered for vitality and worker involvement. This is a formidable list of “musts,” but all of these elements are necessary to adequately support an effective FOD control effort.
Without a dedicated unit to conduct these activities, the burden on any other organizational unit(s) is difficult, if not impossible, to support. Many companies have tried part-time programs, with FOD Monitors assigned to check work areas at intervals during and at the end of each shift, but these efforts are weak at best. If this approach is used, volunteers should be solicited, not appointed at random. Even when executed and controlled by a conscientious FOD supervisor or coordinator, a part-time FOD effort in manufacturing facilities invariably falls short of a staffed full-time unit.
There is no other way to say it: Effective FOD Prevention is an investment and a commitment.
The number of people required to support a full-time FOD effort will vary depending on the type of operation, number of aircraft in production, the level of FOD control required, and of course, budget available. As a rule of thumb, consider having an inspector for every five aircraft in production. In addition, a clerk to handle data entry/retrieval and a supervisor/manager to oversee the operation is necessary. FOD is serious business. Don’t try to avoid doing it right. Appoint a fully staffed FOD department and give it the authority, support and tools needed to do the job without compromise.
Because aircraft have so many difficult areas to inspect and clean, specialized equipment and tools are necessary to assure a FOD free product. Some manufacturers rotate or shake the entire aircraft assembly at various stages to dislodge foreign objects, but a flashlight and mirror can only go so far. Specialized equipment is necessary to verify cleanliness.
One of the most valuable tools to inspect and retrieve FOD is the borescope. This tool was originally developed to inspect within the human body but is now used in many industrial applications to perform inspections that otherwise would not be possible without dis-assembly or destruction.
Numerous companies build borescopes that are ideal for aircraft inspection and cleaning. A wide variety of borescopes are available with specialized uses; some are designed for engine inspection, some have articulating tips with FOD retrieval capability and some are ideal for fuel cell inspection with explosion-proof lighting units.
It is important to consider the safety aspects of the area to be inspected before deciding on the borescope to be used. Never use a borescope on electrically powered circuits. It is recommended that aircraft batteries be disconnected if there is any chance of electrical contact or shorting. Not only can aircraft components and the borescope be damaged, but personal injury to the borescope operator is also possible.
Limit the use of borescopes to those persons trained in the operation, maintenance and safety characteristics of the equipment. Borescopes are expensive and fragile; improper care or use can easily damage or destroy this valuable tool. It is recommended that borescopes be used only by the FOD Department personnel, who should keep the equipment under lock and key when not in use.
It is one thing to locate FOD, it’s quite another to remove it.
Ingenuity is often required. Sometimes FOD cannot be removed and must be secured with sealant to assure it will not migrate or get loose. Long extension tubing can be affixed to a sealant gun to perform this operation.
Other FOD inspection/removal tools needed include pneumatic powered vacuum cleaners with extension suction tubes, mirrors, high intensity lights, magnets and a variety of “FOD grabbers.”
Within the manufacturing environment, FOD controls vary with the type of work being performed.
Although all share the same key elements of control, each category differs enough to allow diversity within the control methods.
Rules that apply to the flightline may not be practical in a backshop. For supervisors and workers to support the FOD Program, they need to understand the importance of the controls and acknowledge that they are reasonable given the work at hand.
Often called “backshops,” these are work areas such as sheet metal, machine shop, tubing and electrical harness. Typically, these shops do not have enclosed panels or components; therefore, FOD control is less critical than in other manufacturing areas.
These are areas where fabricated parts are put together and cavities are enclosed with fasteners or sealant. These areas require greater control and more frequent inspections and cleaning than Fabrication areas. All areas or panels “closed out” should have a FOD buyoff (inspection) on the paperwork (documentation of process).
This requires the highest level of control because the product is in its final stages preceding delivery or flight. Assurances must be made that all personnel entering the work control area remove all loose/unsecured personal items, e.g., watches, keys, jewelry and coins, and account for all tools and hardware carried near the product. A tool/ hardware inventory form may be required in certain FOD-critical products or areas.
It is important to clearly define the control areas so there is no question about which rules apply. Also, keep in mind that work “travels” when not completed in its designated area. For example, a component not completed or available in assembly must be installed in checkout/test. Typically, the worker who normally installs the component in assembly is the one who “travels” to checkout/test to install the part. Therefore, it is critical that all workers who may function in another control area be familiar with the FOD control requirements for any area in which they may work. Training, SOPs, signs and supervisors of each process must learn and support the differing rules for each control area.
The key elements of FOD Prevention are universally accepted but applied in various ways throughout the aerospace industry. To cooperate with the control areas addressed above, each element must be dissected and articulately defined to allow clarity and ease of enforcement. The better defined, the better understood. The better understood, the better compliance.
Posters and other visual reminders should be used to promote the rules. Everyone working at the facility should know and understand the key elements… including security personnel.
You know your FOD Awareness Program is working when a washer is retrieved from the shop floor and reported by an administrative clerk! The key elements are something to advertise. Don’t keep them hidden in a procedure folder or meeting room.
Plaster them on the walls, publish info bits in the company newsletter or on the intranet, make up or purchase FOD stickers to put on toolboxes and work benches, have poster contests, give recognition awards for compliance and do anything else you can think of to keep people focused.
The key elements are easy to remember because they are so integrated within the manufacturing workplaces: Tool Control, Hardware Control, Product Protection and “Clean-As-You-Go.” Keeping the rules simple is important. So is defining their specific applications, as you can see from the following Chart.
FOD Table
Letter Codes for the three control areas are:
F = Fabrication
A = Assembly
C = Checkout
FOD control in any manufacturing facility depends on a clean, well-organized work environment. Workers need designated areas for tools, storage and cleaning equipment.
Planning for efficiency may involve removing unnecessary items, relocating benches, equipment, storage units and toolboxes to facilitate smooth workflow and logical sequencing. Shop floors should be painted a light color to allow easy identification of dirt/debris and also to facilitate cleaning. Designated spaces for cleaning equipment, trash containers, ladders, air hoses and toolboxes should be outlined and labeled on floors and walls.
Believe it or not, some workers will claim that they didn’t clean up because they couldn’t find a broom. It is important to have everything returned to its place when the task is completed so that it can be found easily when needed.
Signs that outline FOD controls for each work area should be prominently posted so no one questions the rules. Visibility boards to display FOD metrics, bulletins and awareness media should be staged in each work center so that workers have information and feedback related to performance and goals.
Many manufacturing companies have adopted the Five S’s of Housekeeping as an aid for workplace organization. It is a concept that can be adapted to meet the needs and level of involvement desired. The following outline is one derivation that has been used successfully:
The process of removing unnecessary items from the workplace.
Identify uniform methods to maintain work areas
Provide specific, understandable directions, and procedures.
Establish routines/requirements to maintain cleanliness.
Identify individual responsibilities.
Ultimately, the judge of your FOD Program will be the customer. Solicit feedback by requesting them to identify any foreign objects found in the delivered product and the exact location or zone. Provide a corrective action response to demonstrate that you are attentive to their needs; specify what has been implemented to eliminate the error from future deliveries. With all deliveries, include missing item reports for any items not found or retrieved during the entire manufacturing process.
Invite the customer to visit the factory on a regular basis. Communicate the importance of keeping FOD out of the product. Workers sometimes lose sight of the fact that the work they perform everyday has serious implications related to quality, safety and reliability. Reminders, especially from the customer, are usually well received and understood.
The “customer” concept works well to control FOD in-house before it gets to the final customer. Develop this by using promotional and awareness training sessions to build a “customer focused” culture within your manufacturing facility. Each work center or department should consider themselves the “customer” of the preceding department. As the component or assembly moves from one work center to another, it then receives a FOD check before leaving, and another acceptance FOD check at the receiving “customer” work center. Items found by the receiving unit’s inspection should be documented and reported to the sender for corrective action. The report should also be forwarded to the Manufacturing Manager and the FOD Program Manager who will monitor the timeliness and effectiveness of the corrective measures. Work centers that do not find FOD in their acceptance inspections are then responsible for any FOD found by their customer down the line. Work centers with the best customer deliveries should be recognized in some formal way monthly and group awards given to the best work center of the year. This approach to FOD Prevention not only controls FOD, it creates a competitive, team-focused environment of building quality products.
“Quality” is the buzzword that implies reliability, integrity, safety and customer satisfaction. Without an effective FOD Control Program in the manufacturing arena, the product will not meet quality standards. Eventually sales will fall, contracts will be lost or not awarded and accidents/incidents become more likely. Achieving quality is not easy but every effort must be made to get there. As one company achieves higher quality, the challenge is greater for all others, and so the race continues to everyone’s benefit.
Don’t be left behind. Jump on the Zero FOD bandwagon and don’t accept anything less. Remember: FOD can’t be inspected out at the end of the line… processes must be in place throughout the entire build cycle to assure that it doesn’t get in.